For Immediate Release
Contact: Daniel Wackershauser, Marketing and PR Specialist
Phone: 608.822.2303
Mail: 1800 Bronson Blvd., Fennimore, WI 53809
Date of Release: October 12, 2022
Economic leaders on campus to discuss manufacturing grant
Fennimore -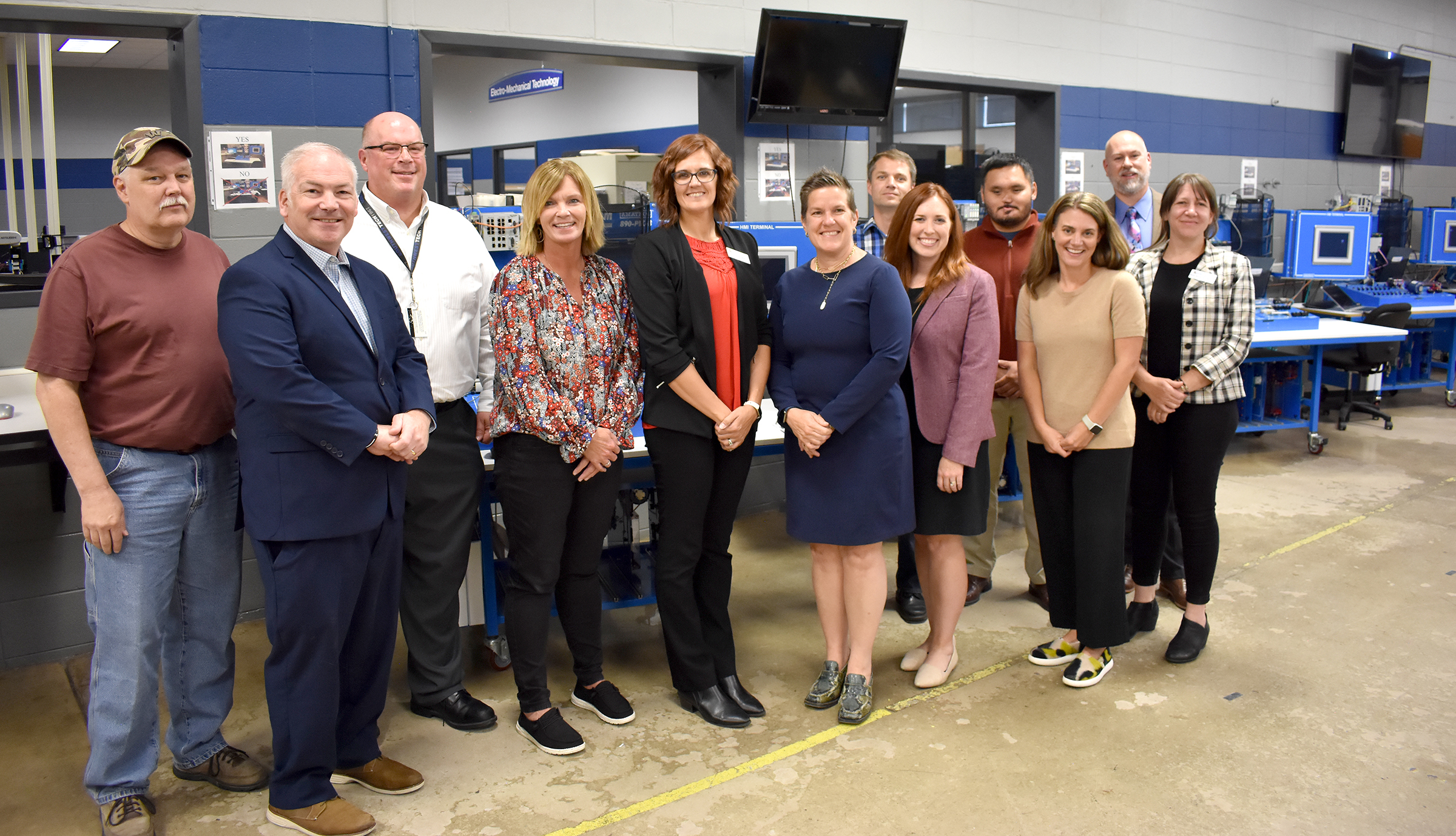
(L-R) Mike Berg, Plant Manager, Imperia; Jamie Nutter, Executive Director, CESA #3; Dennis Cooley, Director of Business and Industry Services, Southwest Tech; Tina Stoeffler, Vice President of Operations, Truvant; Holly Straka, Business and Industry Services Specialist; Missy Hughes, Secretary and CEO, Wisconsin Economic Development Corporation; John Fick, EDA University Center Coordinator, UW-Platteville, Danielle Williams, Assistant Deputy Secretary, Department of Workforce Development; Jobert Bermudo, Electro-Mechanical Technology Instructor; Erin Arango-Escalante, Administrator, Division of Early Care and Education, Department of Children and Families; Derek Dachelet, Executive Dean, Southwest Tech; and Amy Seeboth-Wilson, Director of Grants, Southwest Tech.
Wisconsin economic leaders joined partners at Southwest Wisconsin Technical College on Oct. 5 to discuss a recently-awarded Workforce Innovation Grant (WIG). Southwest Tech is part of a consortium that received a $2.9 million grant. The consortium, Advance Southwest Wisconsin, is designed to help businesses in Crawford, Grant, Iowa, Lafayette and Richland counties train more than 518 employees, hire another 342, and promote at least 68 incumbent workers in three years through custom upskill training, advanced tecnhology expertise, and targeted employee support.
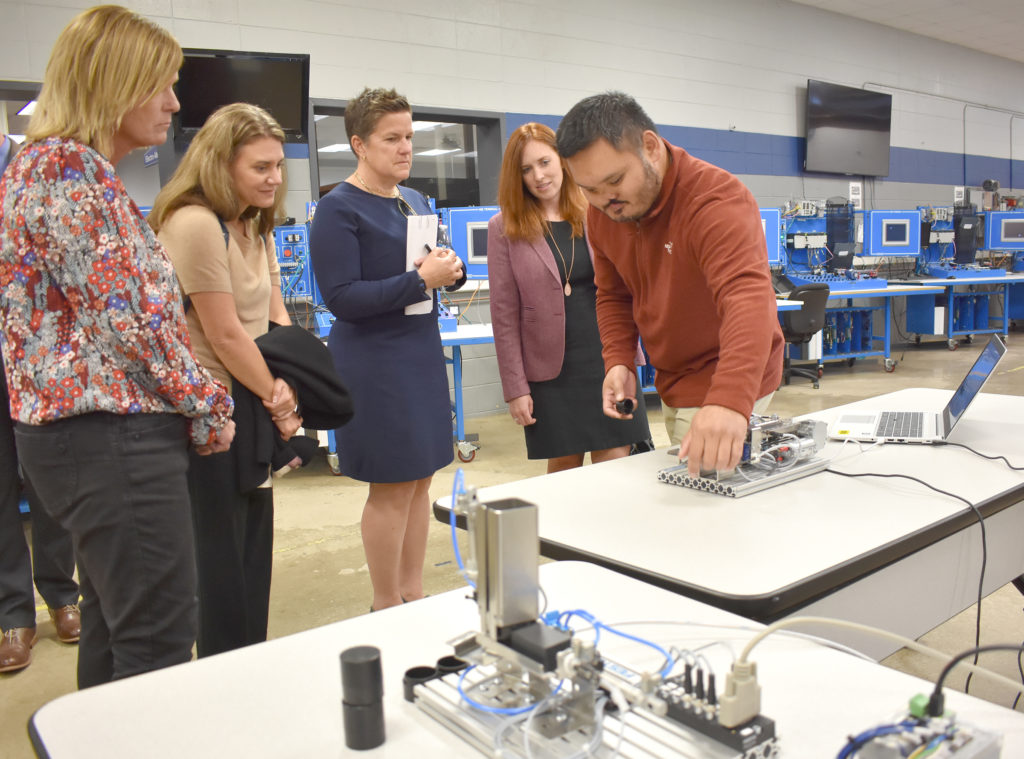
Jobert Bermudo, Electro-Mechanical Technology Instructor at Southwest Tech, demonstrates some of the instrument controls in a lab area on campus.
A group of individuals representing Gov. Tony Evers’ office, Southwest Tech, the Wisconsin Economic Development Corporation, Wisconsin Department of Workforce Development, the Wisconsin Department of Children & Families, CESA #3, UW-Platteville, and local industry, held a roundtable discussion on campus, laying out the obstacles that lay ahead, as well as the opportunities and the projects that can be accomplished through this grant funding.
Among those in attendance was Missy Hughes, secretary and CEO of the Wisconsin Economic Development Corporation. She has been traveling throughout the state, listening to grant recipients discuss how they are going to utilize these funds. “This is a great opportunity to hear what you’re working on and hear what your obstacles are,” she said.
The driving force behind the grant is the rising number of retirements in the manufacturing sector and the difficulty in hiring replacements, as well as the need to upskill workers. During the pandemic, more than 29-percent of area employees over age 55 decided to retire – causing area employers to lose workers with decades of experience. This challenge is most concerning in the manufacturing sector, as the area’s third largest employer. At the same time, the manufacturing rebound has been sharper than expected, with the industry looking to fill 200 new positions above pre-pandemic levels in the next year in southwest Wisconsin. “Advanced manufacturing is critical to our area,” said Jamie Nutter, executive director, CESA #3.
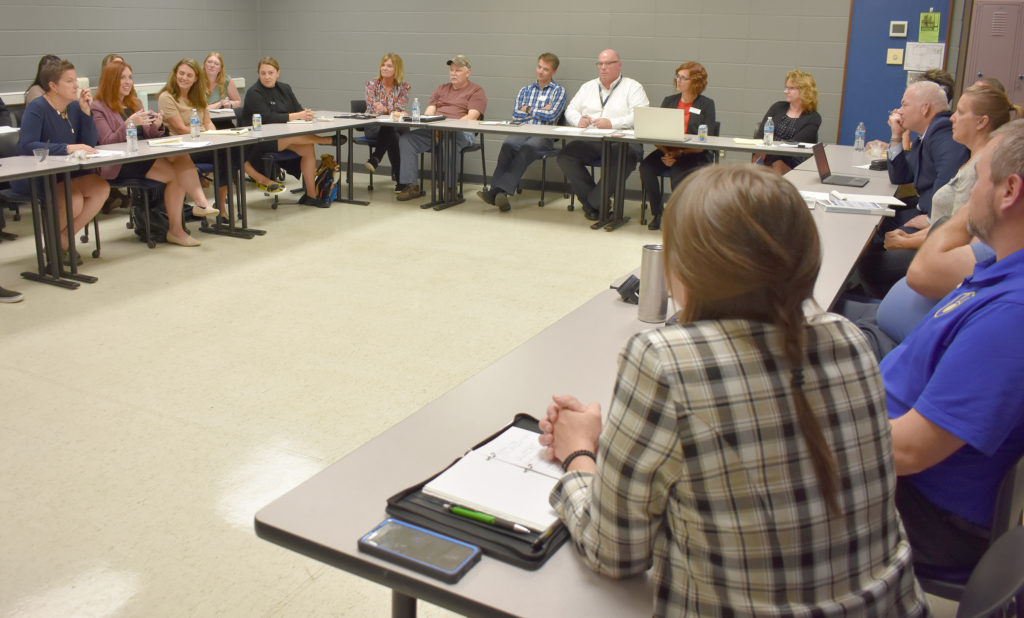
A cross-section of economic, industry and education leaders met at Southwest Tech last week to share their plans associated with the state’s Workforce Innovation Grant.
Focus groups of manufacturing workers by Southwest Tech identified three main gaps in the local workforce ecosystem:
Gap 1: Current manufacturing employees lack the skills necessary to replace the older, retiring workforce, many of whom were managers or highly skilled technicians.
Gap 2: The lack of regional expertise in advanced technology. The industry had changed significantly in the last decade, and manufacturers want to compete globally.
Gap 3: The most vulnerable workforce faces unique barriers to enter manufacturing – including childcare, transportation, language, and basic educational skills – which all result in higher employee turnover.
According to Derek Dachelet, executive dean at Southwest Tech, as Advance Southwest Wisconsin moves forward through the grant, the focus will be on incumbent workers and special populations. “The Workforce Innovation grant will allow us to better serve workers who are interested in exciting, family-supporting jobs enter the manufacturing workforce and upskill existing workers with new skills to advance their careers,” he said.
Southwest Tech will provide onsite trainings to quickly address skills-gap needs. The trainings will include tech skills like machine and program logic controls using the college’s state-of-the-art mobile training unit, and supervisory skills such as LEAN principles. Also included will be Spanish for the Workplace, safety, compliance, and more. “Manufacturing is one of the best-paying jobs in the region,” said Amy Seeboth-Wilson, director of grants at Southwest Tech. “We want to help elevate people in southwest Wisconsin to those well-paying jobs.”
In addition, all three of the regional educational organizations will meet weekly to coordinate industry support, from launching a new manufacturing and STEM Youth Apprentice program, bridging into Southwest Tech’s technical programs and on into UW-Platteville engineering programs where students can specialize in automation.
To help the most at-risk employees overcome barriers to entry, there will be extended service hours at Southwest Tech’s five outreach centers (Darlington, Dodgeville, Platteville, Prairie du Chien and Richland Center.) Certified instructors provide individualized instruction, group classes and targeted referrals to existing services, including transportation, childcare and education funding, through the Southwest Community Action Program and Southwest Wisconsin Workforce Development Board.
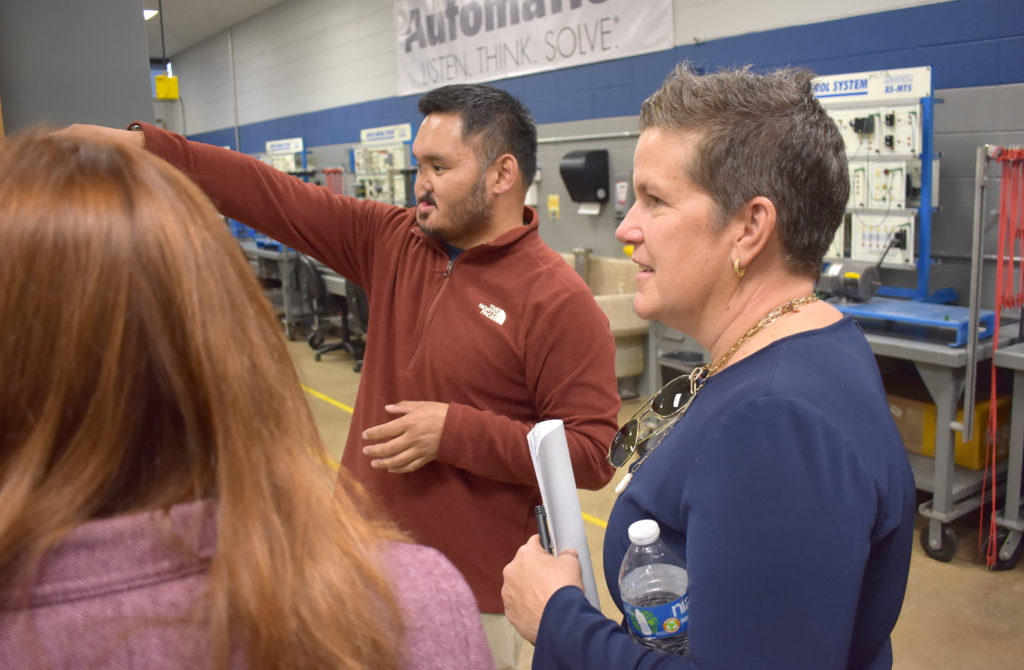
Jobert Bermudo, Electro-Mechanical Instructor at Southwest Tech, gives a lab tour to Missy Hughes, Secretary and CEO of the Wisconsin Economic Development Corporation, and others.
Southwest Tech will be working closely with other education partners, CESA #3 and UW-Platteville. Each of the groups will work in concert, promoting manufacturing careers to their students, and, in the case of Southwest Tech and UW-Platteville, providing necessary training opportunities. John Fick, EDA, university center coordinator at UW-Platteville, noted that many of the high school technical education instructors in Wisconsin earn their educations at UW-Platteville. Through this grant, the university will work to develop automation systems that will help improve manufacturing processes. Employees and educators will be trained in that technology, so they are prepared for the workforce.
CESA #3
According to Nutter, one of many roles of CESA #3 throughout the grant process will be to leverage opportunities to educate students who live in southwest Wisconsin about the rewarding possibilities the region has to offer. “The Wisconsin Youth Apprenticeship (YA) program is a system that is in place to provide high school students work-based experiences to prepare them for careers that are high-wage, high-skill, and high-demand,” he said. “In order to complete a Youth Apprenticeship, high school students must be supervised to ensure they are completing required hours, getting paid at least minimum wage in a qualifying experience, engage in related-instruction, and be evaluated.”
Nutter explained this workforce grant will allow CESA #3 to hire another individual to connect more students to these experiences so that students, parents, and school personnel are more aware of these opportunities and the area sees an increases of YA completers in advanced manufacturing and STEM. “The grant will also enhance the current YA program that allows students to earn up to 12 college credits and related-instruction at no cost to them or their school district,” he said. “The role of CESA #3 is to ultimately have a higher-skilled pipeline to address worker shortages in these two key areas of industry and economic development.”
UW-Platteville
The focus for UW-Platteville through this grant will be on multiple fronts. University officials will add automation curriculum across multiple programs on campus. This will help to train future and current technical education instructors. The main part of the grant funding for the university will allow for enhanced lab settings and a focus on automation training. Currently, there are few programs that focus on how to automate a process. This will help prepare engineering and industrial technology students for the workforce with automation and robotics, according to Fick.
Fick is also excited about the liaison position that will be a part of this grant. If an industry partner has a need, this position will be able to get them where they need to be.
More information about the grants can be found here: https://wedc.org/programs-and-resources/workforce-innovation-grant/.